The goal of this project was to design
and construct a flat-pack furniture structure collaboratively. In addition to considering the packaging style from the start, the design also needed to include two contrasting materials and be created with a budget of $85 each. In addition to these primary constraints, my group mates and I also decided to advance our furniture design by making a modular piece that successfully operates as an individual unit as well as a combined whole.
and construct a flat-pack furniture structure collaboratively. In addition to considering the packaging style from the start, the design also needed to include two contrasting materials and be created with a budget of $85 each. In addition to these primary constraints, my group mates and I also decided to advance our furniture design by making a modular piece that successfully operates as an individual unit as well as a combined whole.
Collaborators:
Jenna Bauer- interior design
John-Paul Kuepper- industrial design
Project Statement
The Trifecta Table, created by Jenna Bauer, John-Paul Kuepper, and Alex Cieslinski, is a side table uniquely designed to adapt to the user’s needs as it can stand on its own or align with other Trifecta tables to create a larger surface area. The combination of wood and acrylic blends natural warmth with modern flair, resulting in a striking aesthetic fusion. Trifecta is a flat-pack product and comes with everything needed to assemble in just a few simple steps.
Iteration and Testing
The testing process for our side table was extensive, but this ultimately helped us in the end because we caught many mistakes and areas for improvement before making final cuts in our actual materials. We began with quarter-scale models, followed by half-scale, and finally full-scale using cardboard to gauge if our sizing was proportionate. All models were laser cut mostly out of chipboard.
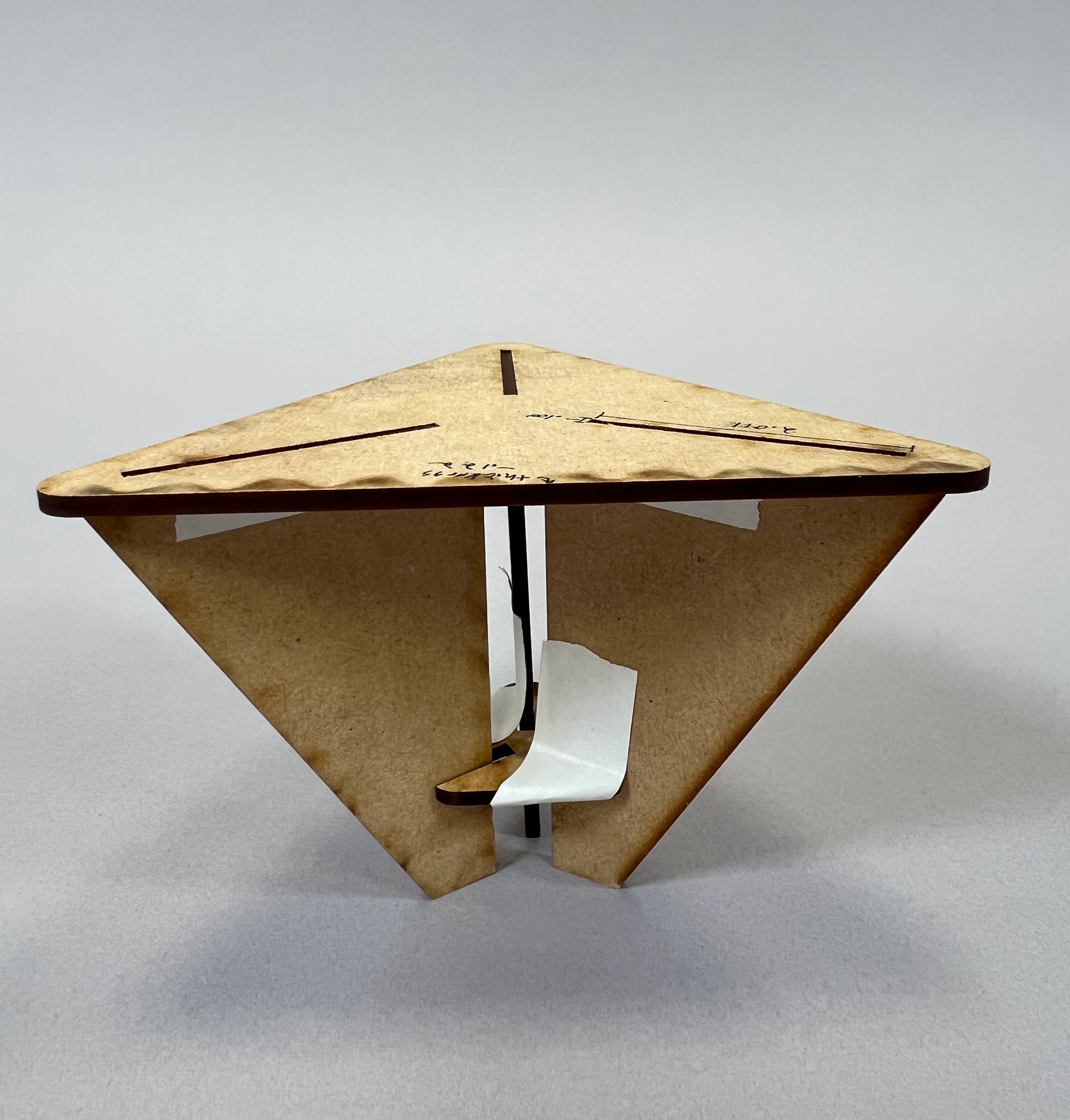
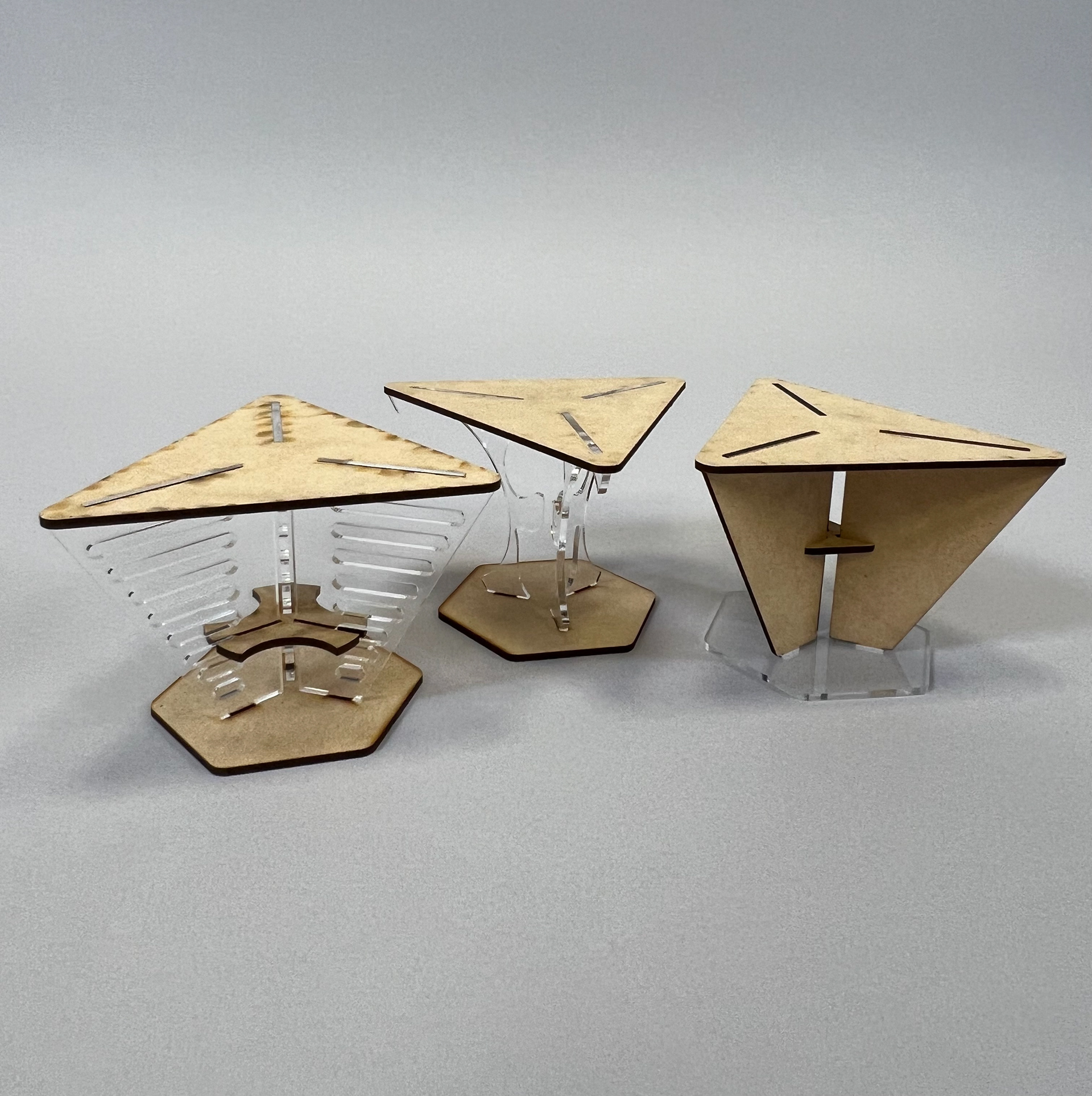
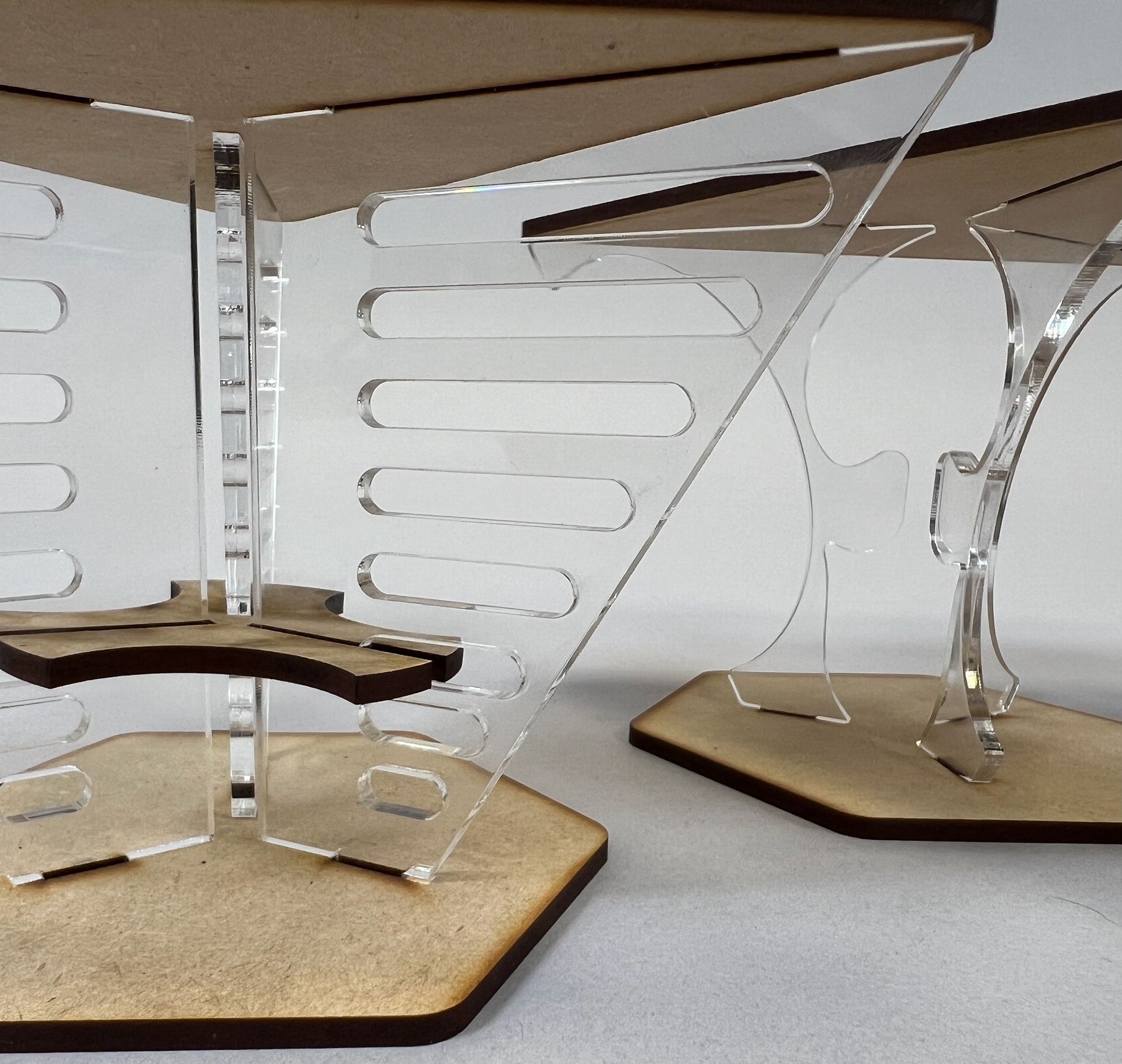
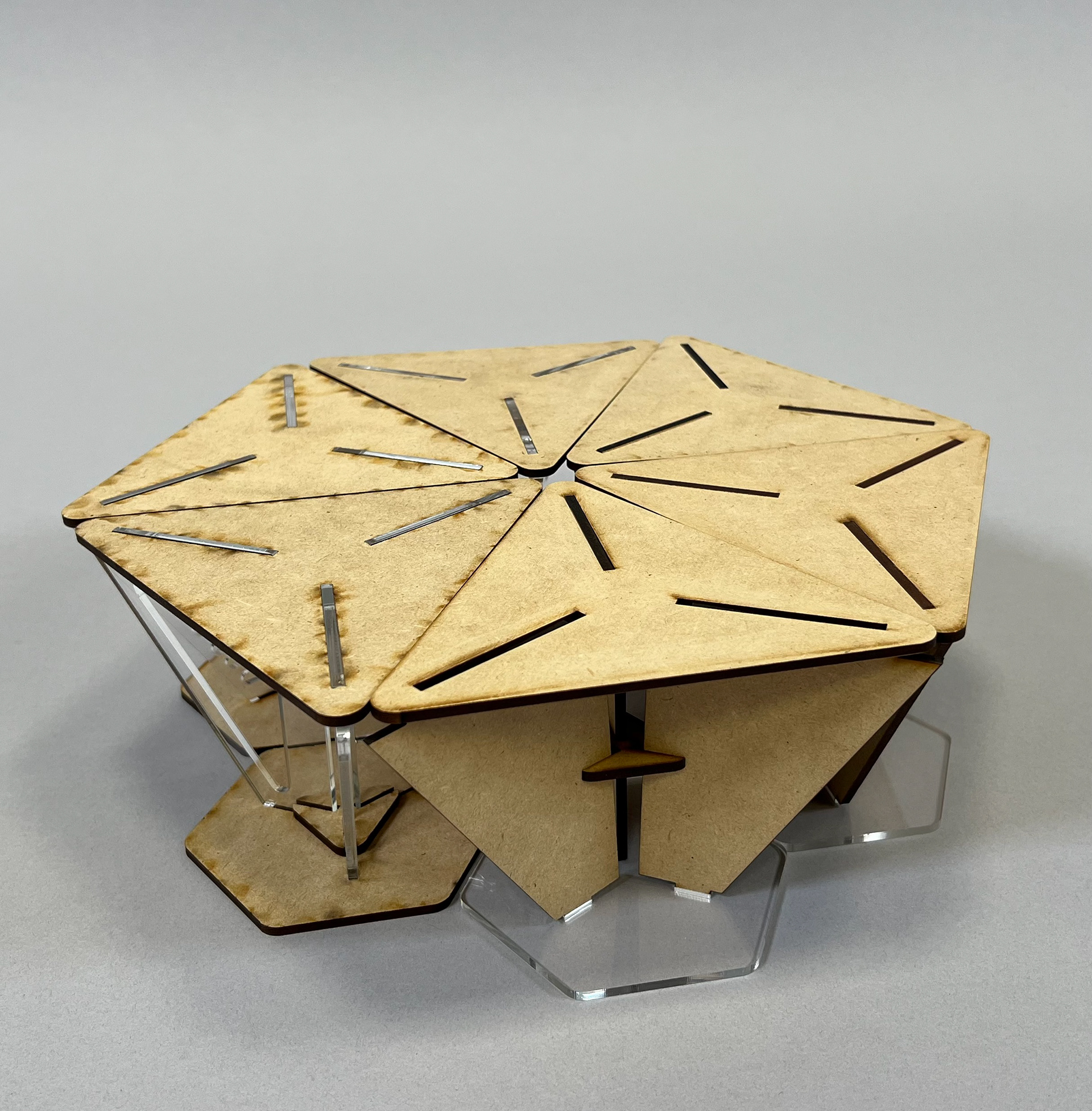
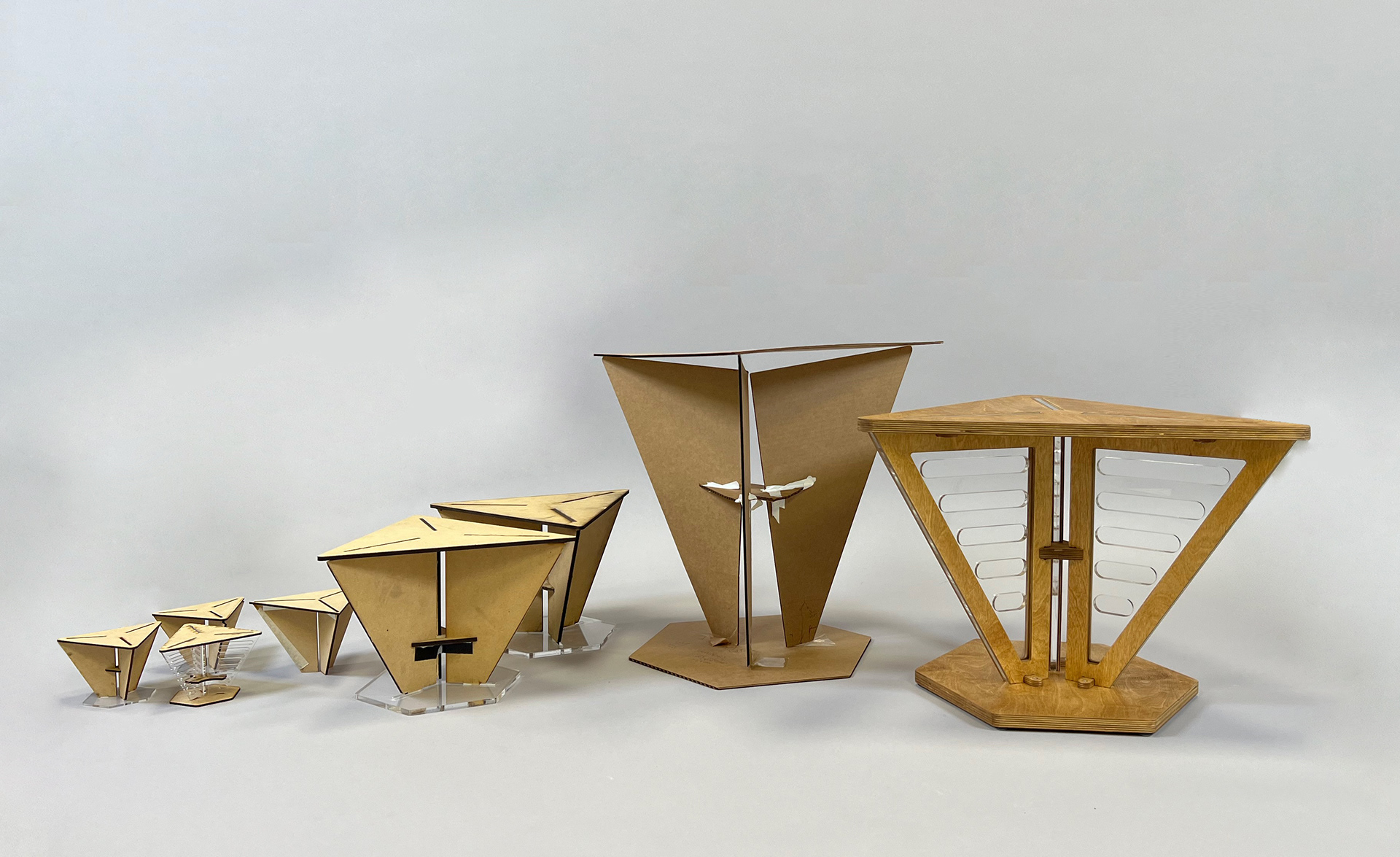
variously scaled models
Materials
Our table design required us to purchase 3/4 inch baltic birch for the bases of the tables as well as 1/4 inch baltic birch for the legs. We slightly adjusted the height of our table legs so that we only needed to purchase one sheet of each thickness. All acrylic used in our tables was given to us at no cost. After purchasing all the finishing items like the finishing oil, threaded inserts, and screws, we all managed to stay within budget per the brief.
Construction
We went into the building phase fairly confident with our design and transferred our cut diagram from Fusion to the CNC machine's software. We did several tolerance tests prior to our final cuts so we could try to eliminate doing extreme amounts of sanding and adjusting after the fact. Unfortunately, even though we did this, the slots in our bases still required a lot of sanding to ensure a snug fit while still being able to be disassembled in order to be packed flat. Because we chose to cut our pieces by machine instead of doing the process by hand, there were certain design choices that we needed to consider such as having a dog bone shape at all corners of the CNC cut due to the round bit it uses to cut. The acrylic however was cut using the laser cutter which can cut sharp corners. It was important to consider all of our options and what consequences each would have in the final look of the table.
After sanding all the pieces down, we decided on a darker finishing oil and applied three coats. The final steps were drilling holes in our bases so we could put in threaded inserts where the locking brackets sit. We also put a counter sink in these brackets last minute primarily to improve the aesthetic and have the screws flush with the wood.
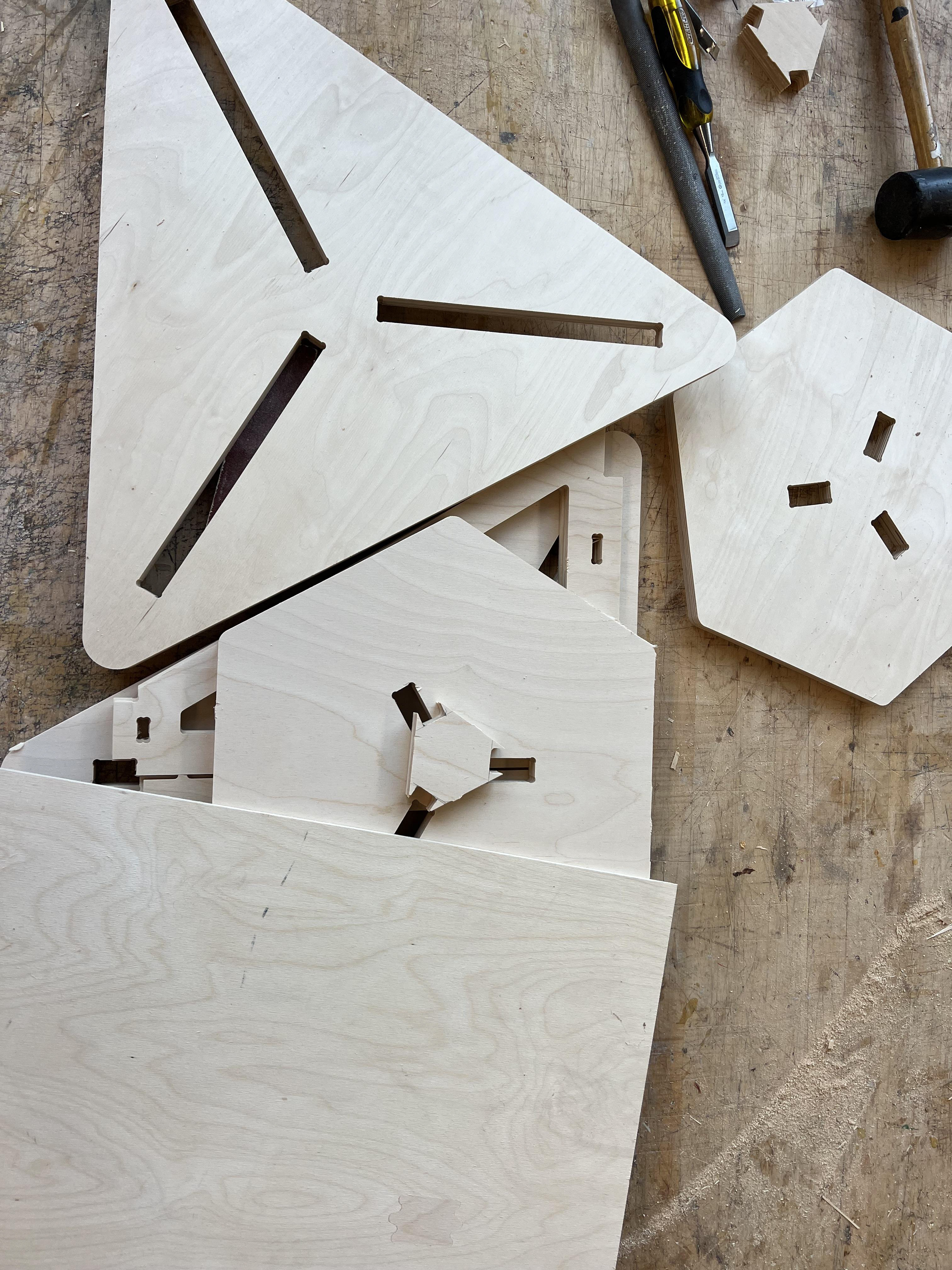
pieces before being stained
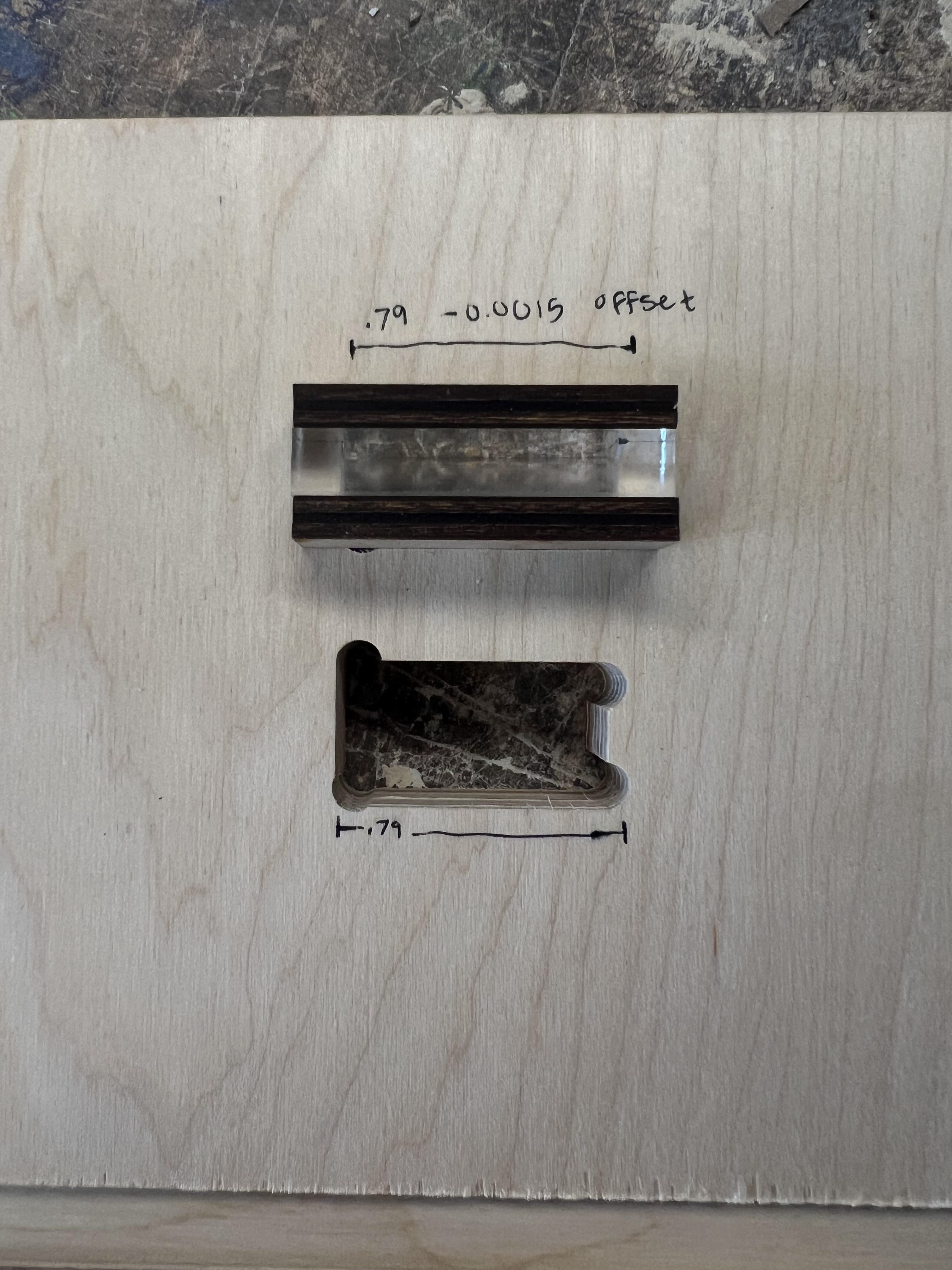
tolerance testing
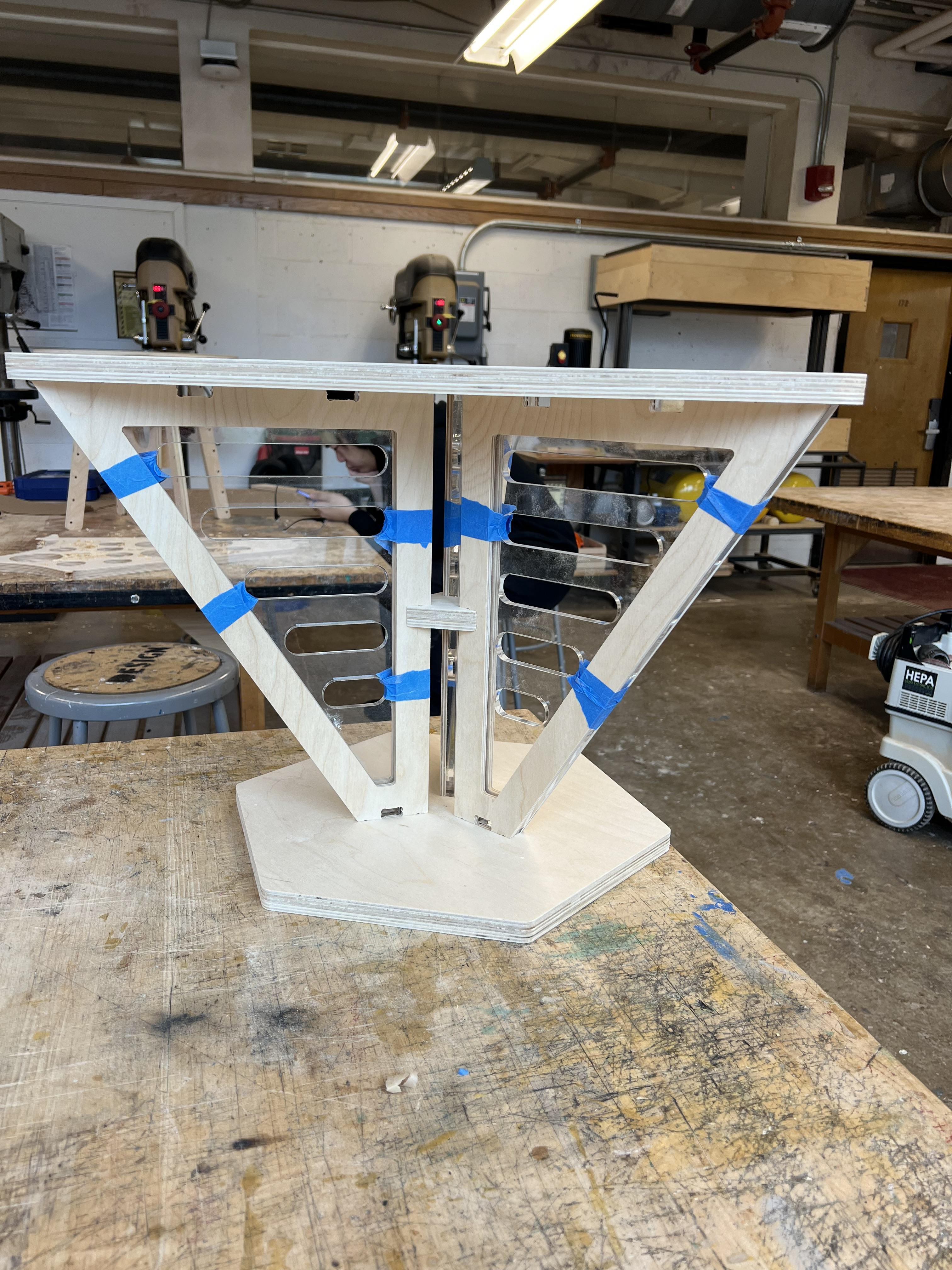
first assembly test
Final Design
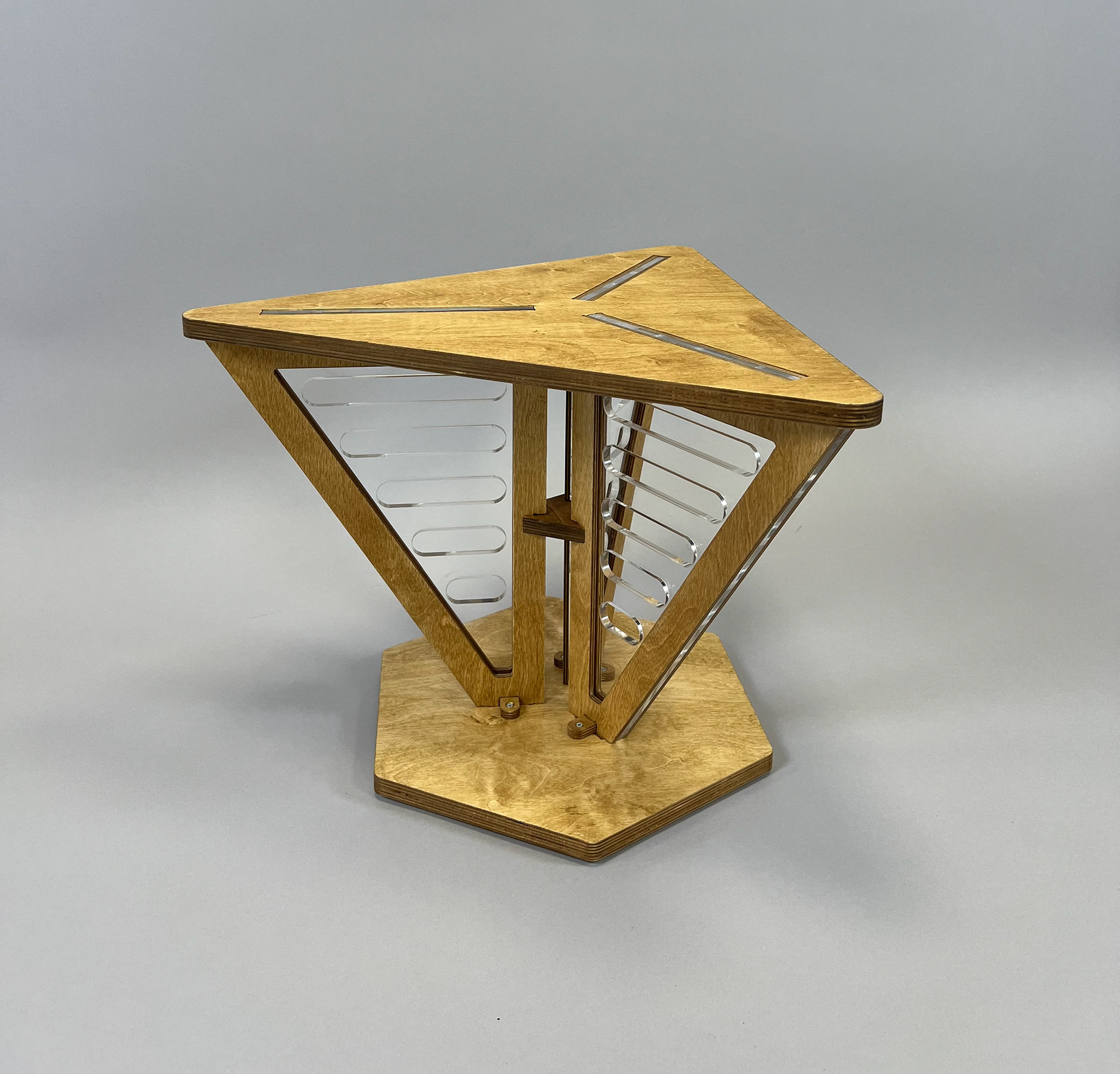
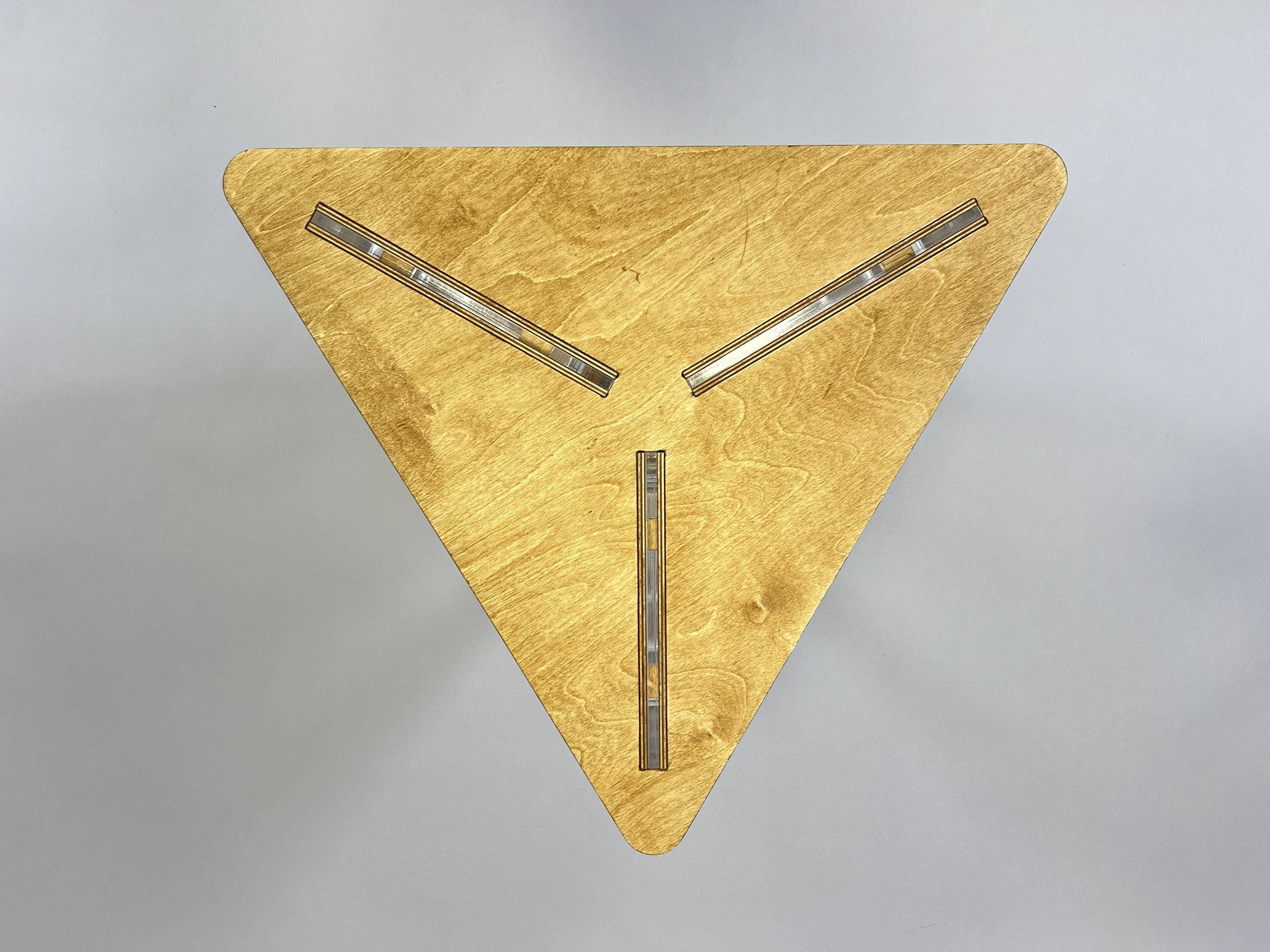
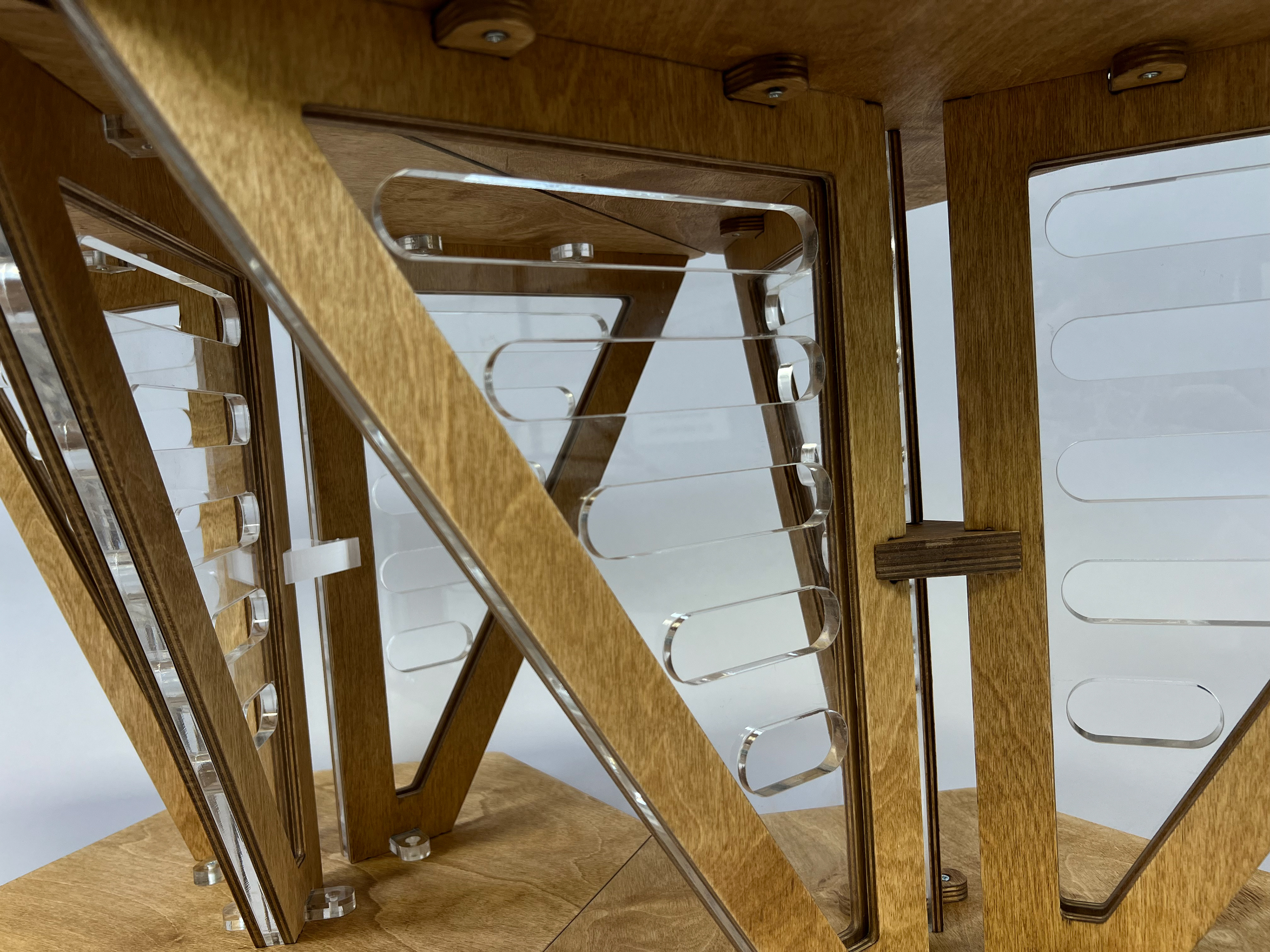
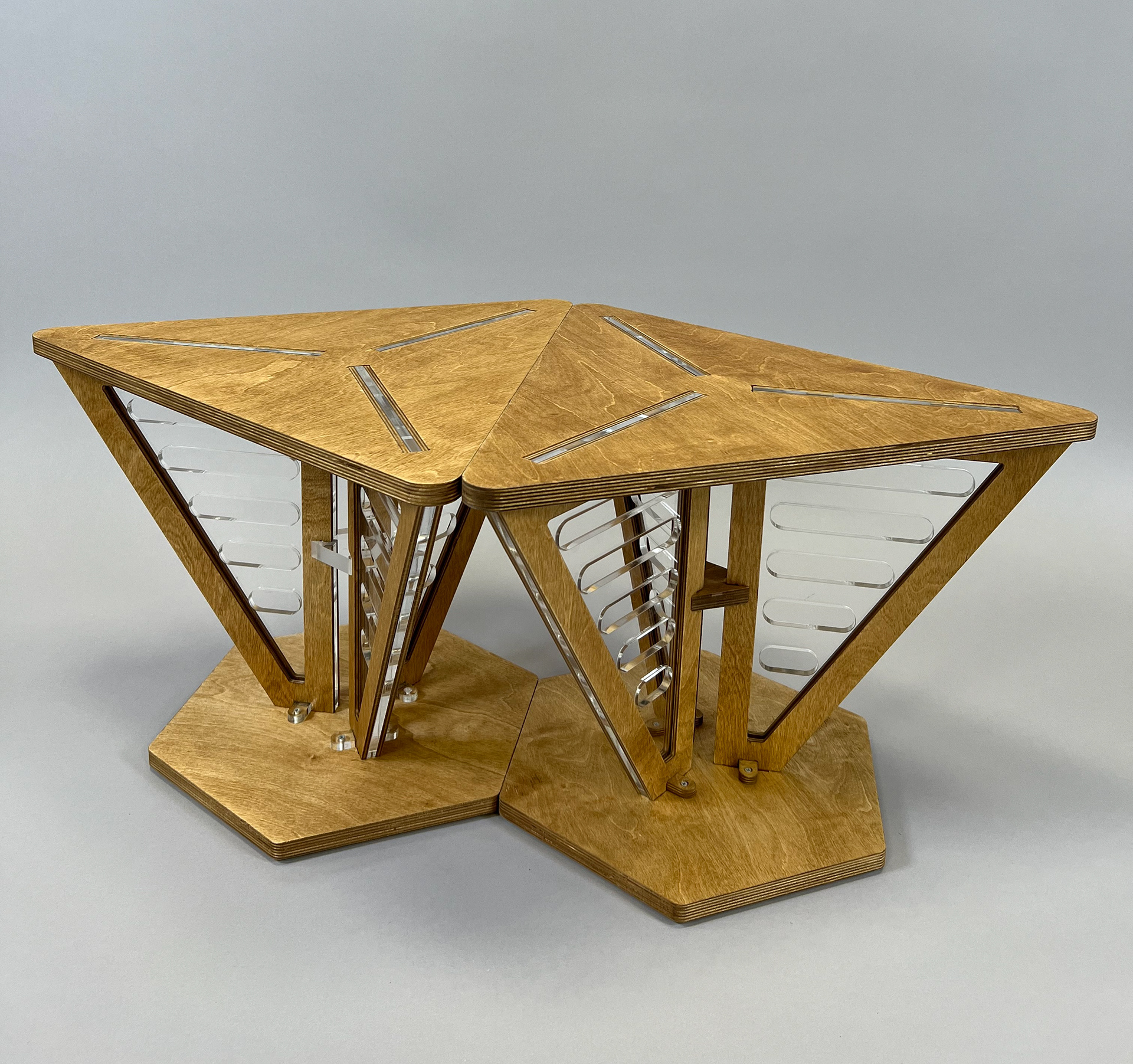
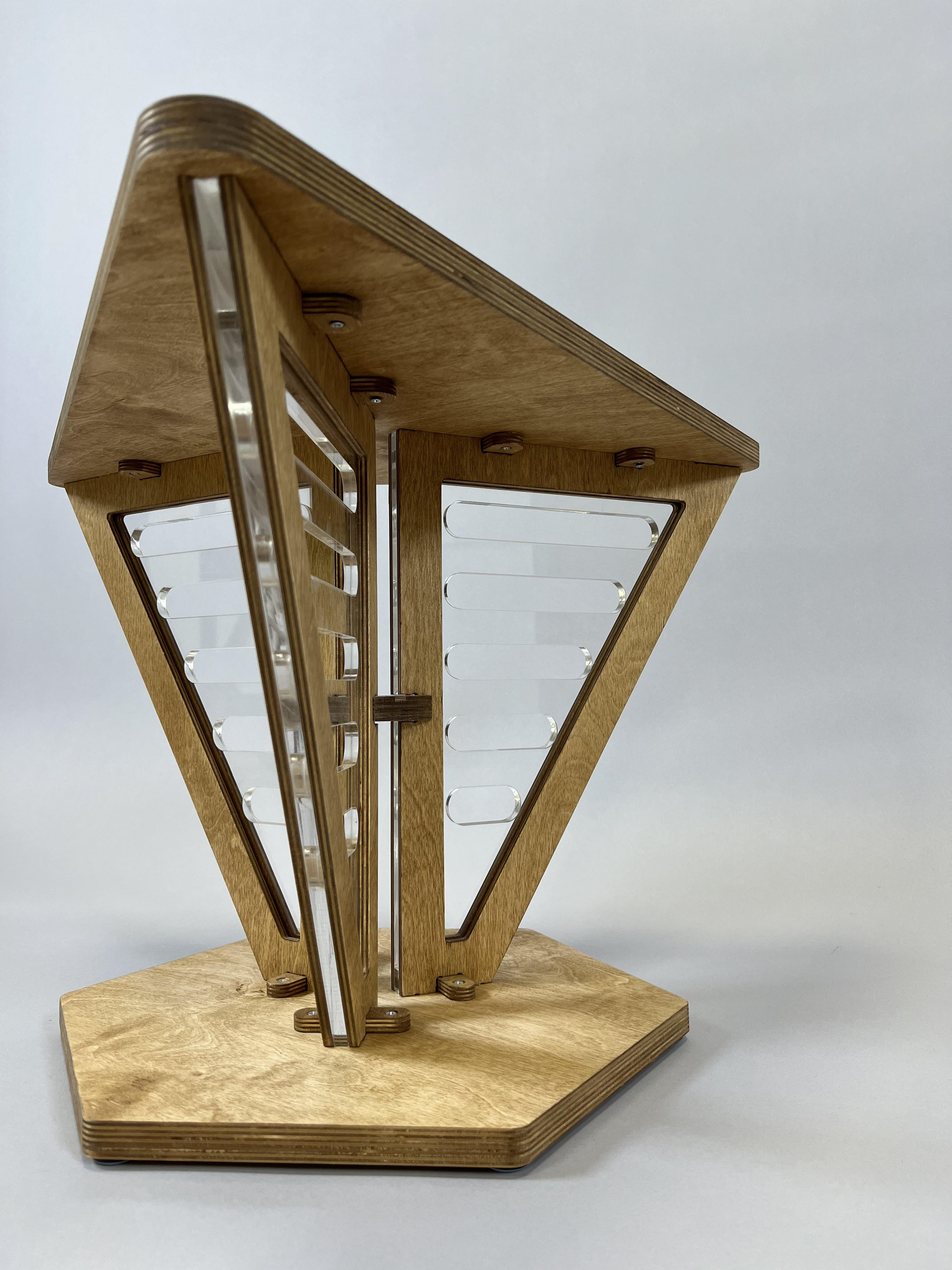
Branding and Packaging
The final phase of this project was to either create packaging for our furniture piece, create brand elements, or provide instructions for the assembly of the product. My team was able to stay fairly on schedule throughout the construction process leaving us with a good amount of time as we neared the end of the term. Because of this, we decided to tackle all three parts of this last phase. The packaging was laser cut out of cardboard in the shape of a triangle since all of our pieces fit within the shape of the equilateral triangle top to the table. This flat packaging is efficient and creates easy storage or shipping. To add some visual interest to the box, we rasterized our cutting diagram and logo onto the top. For the instructions, we took an exploded view of our 3D model in fusion and added arrows to direct assembly. Finally, the name "Trifecta" was inspired by the motif of threes throughout this project- three team members, three sides to the top of the table, and three tables constructed. The logo was designed to mimic the geometry of our tables.
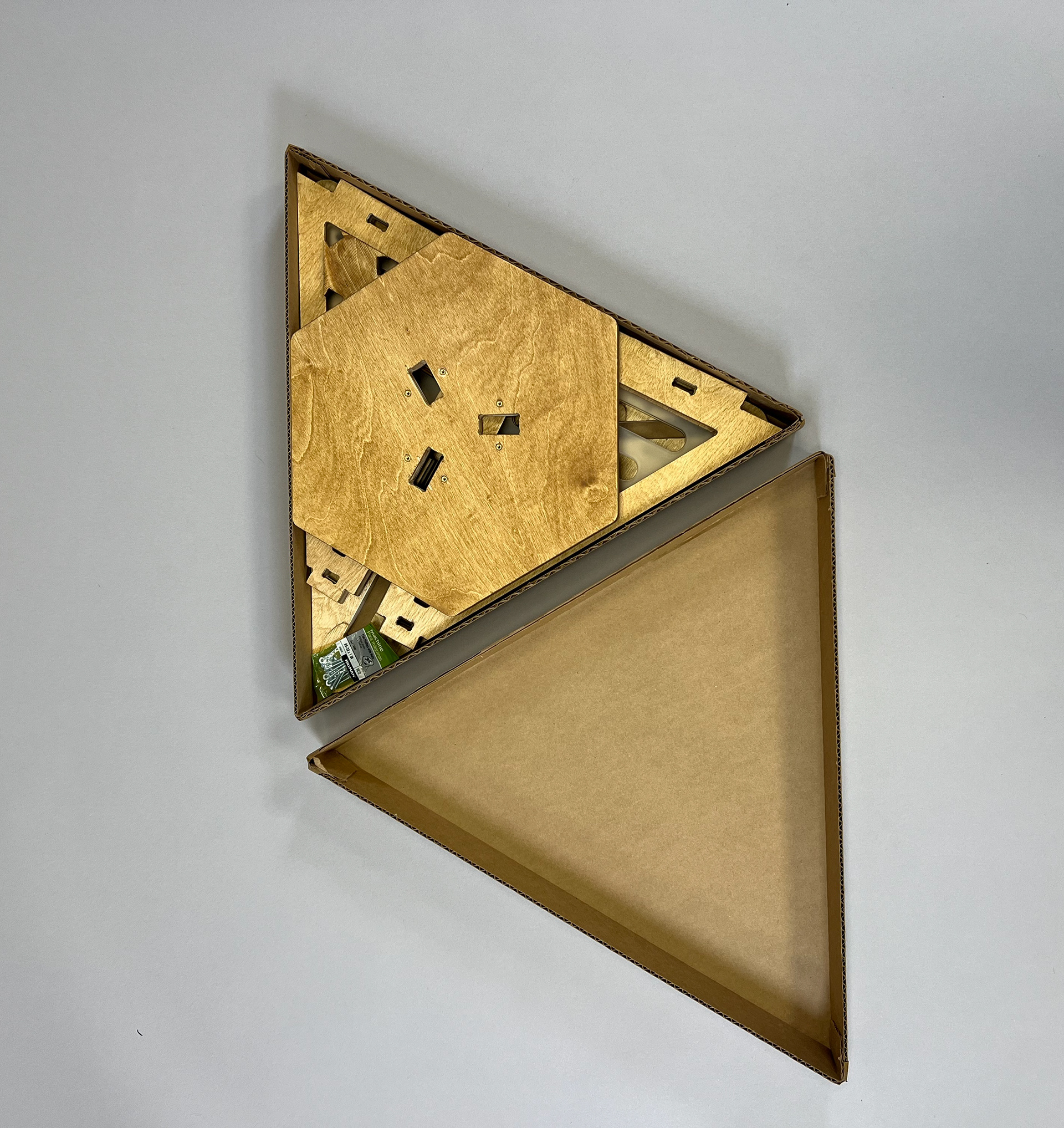
table disassembled and in flat pack
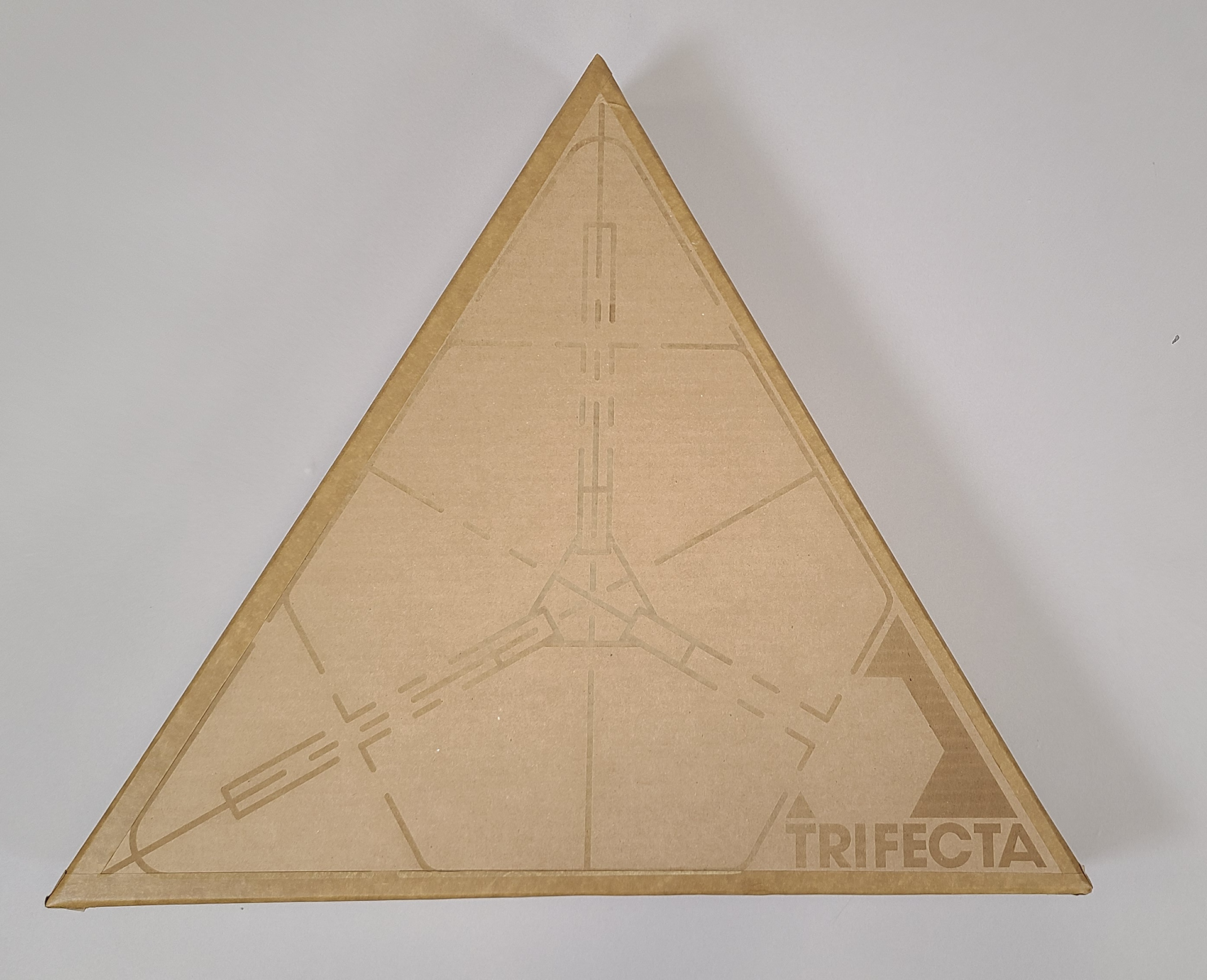
box rasterized with logo
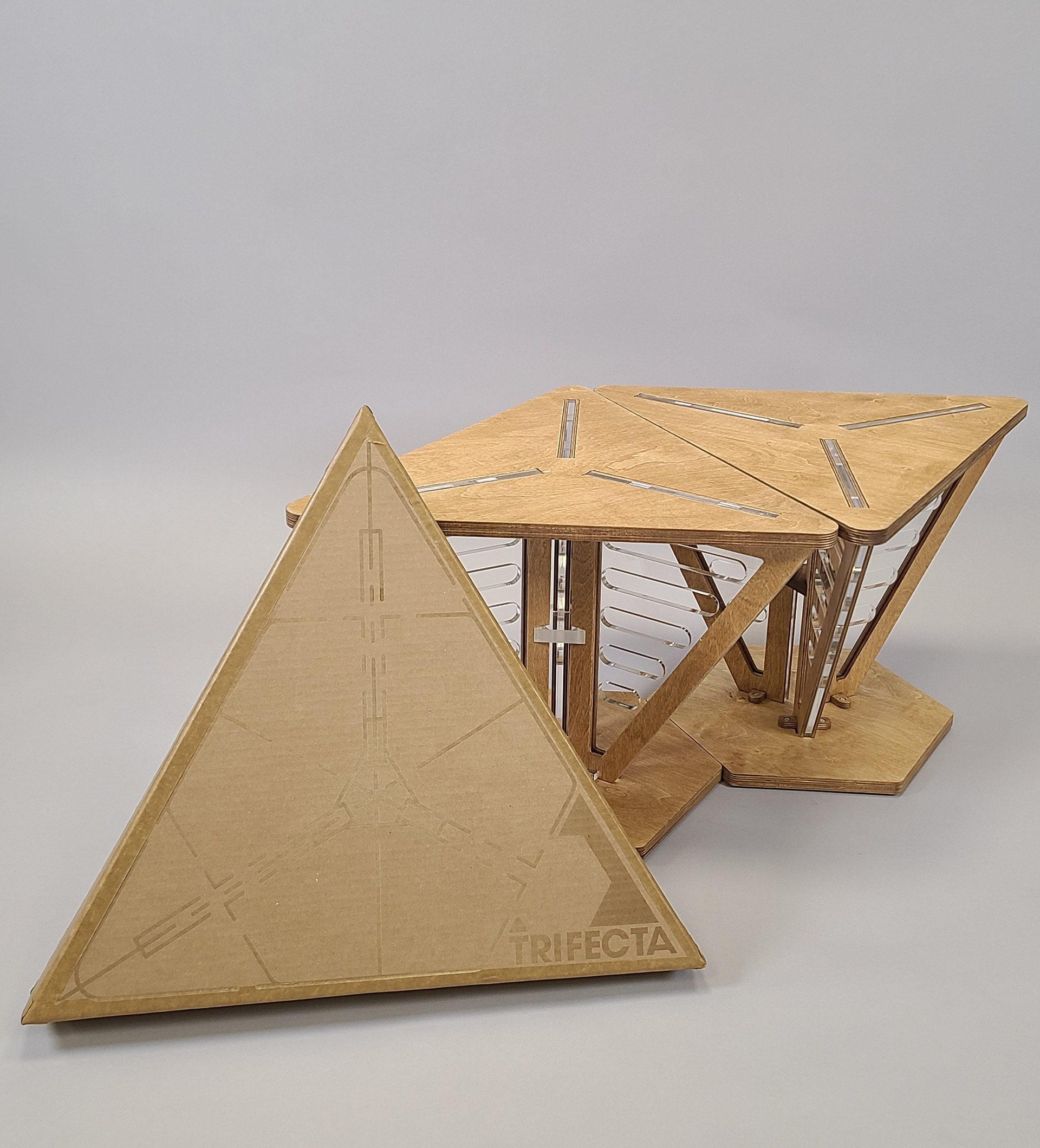
tables and packaging
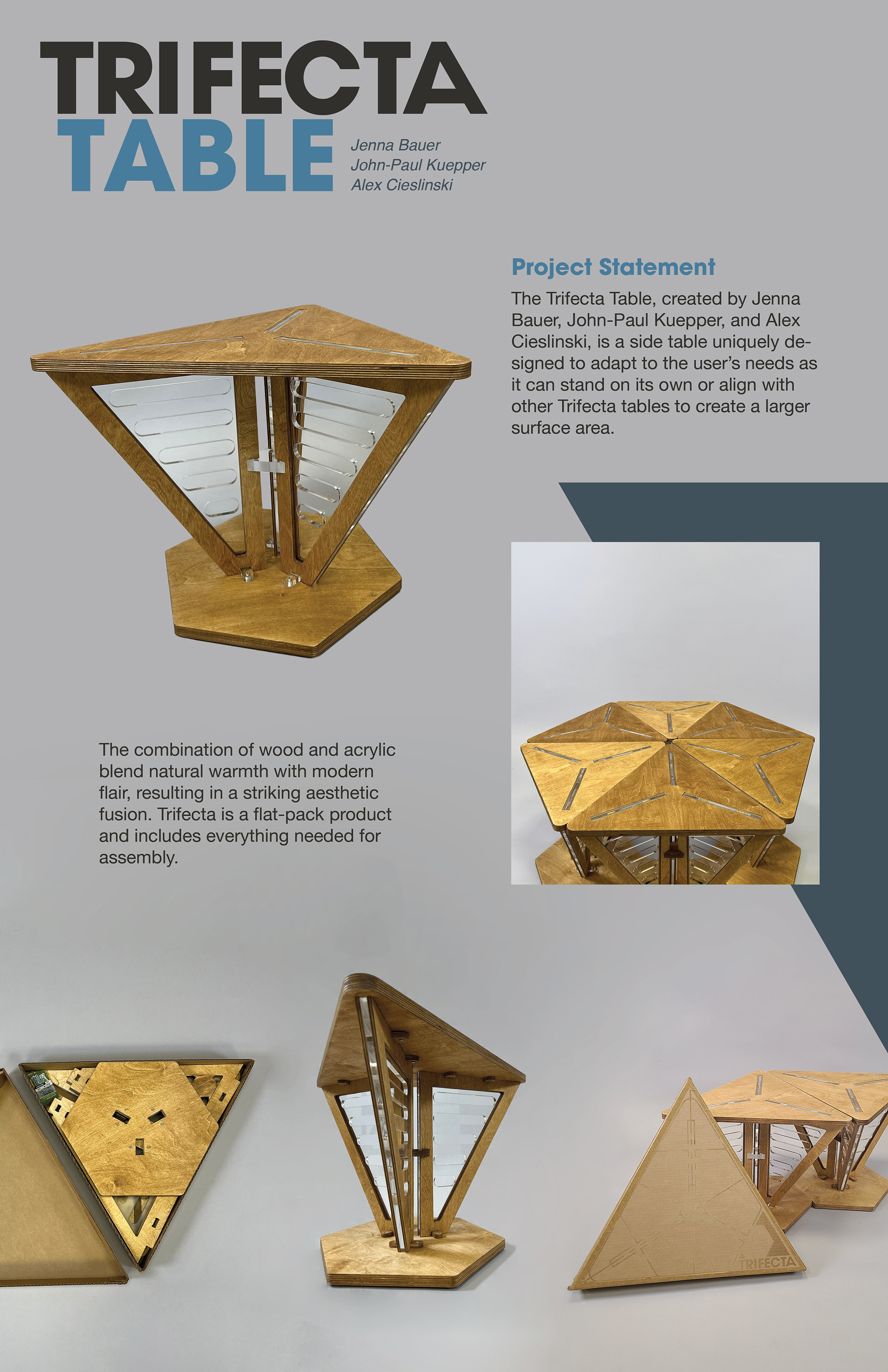
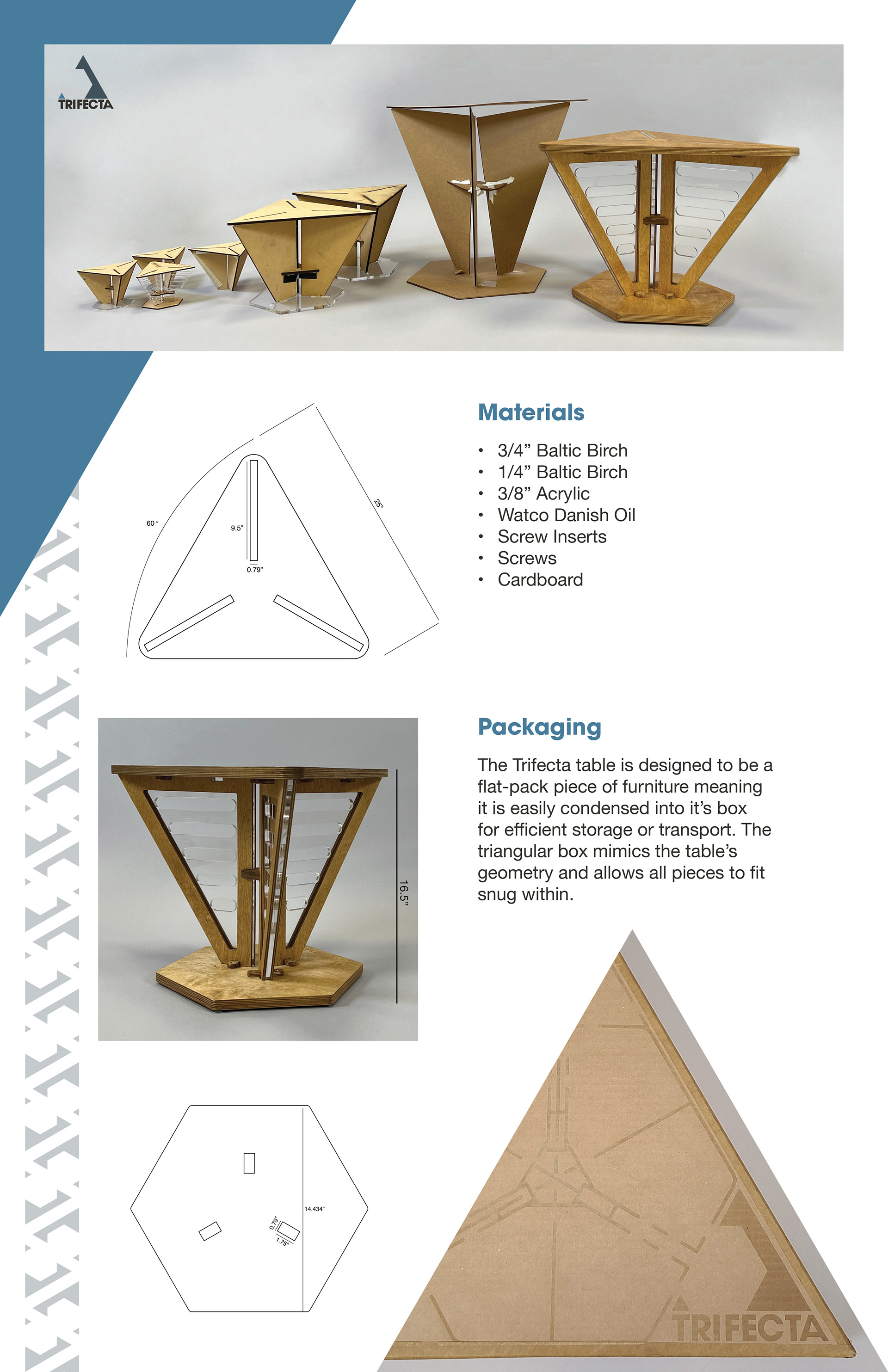
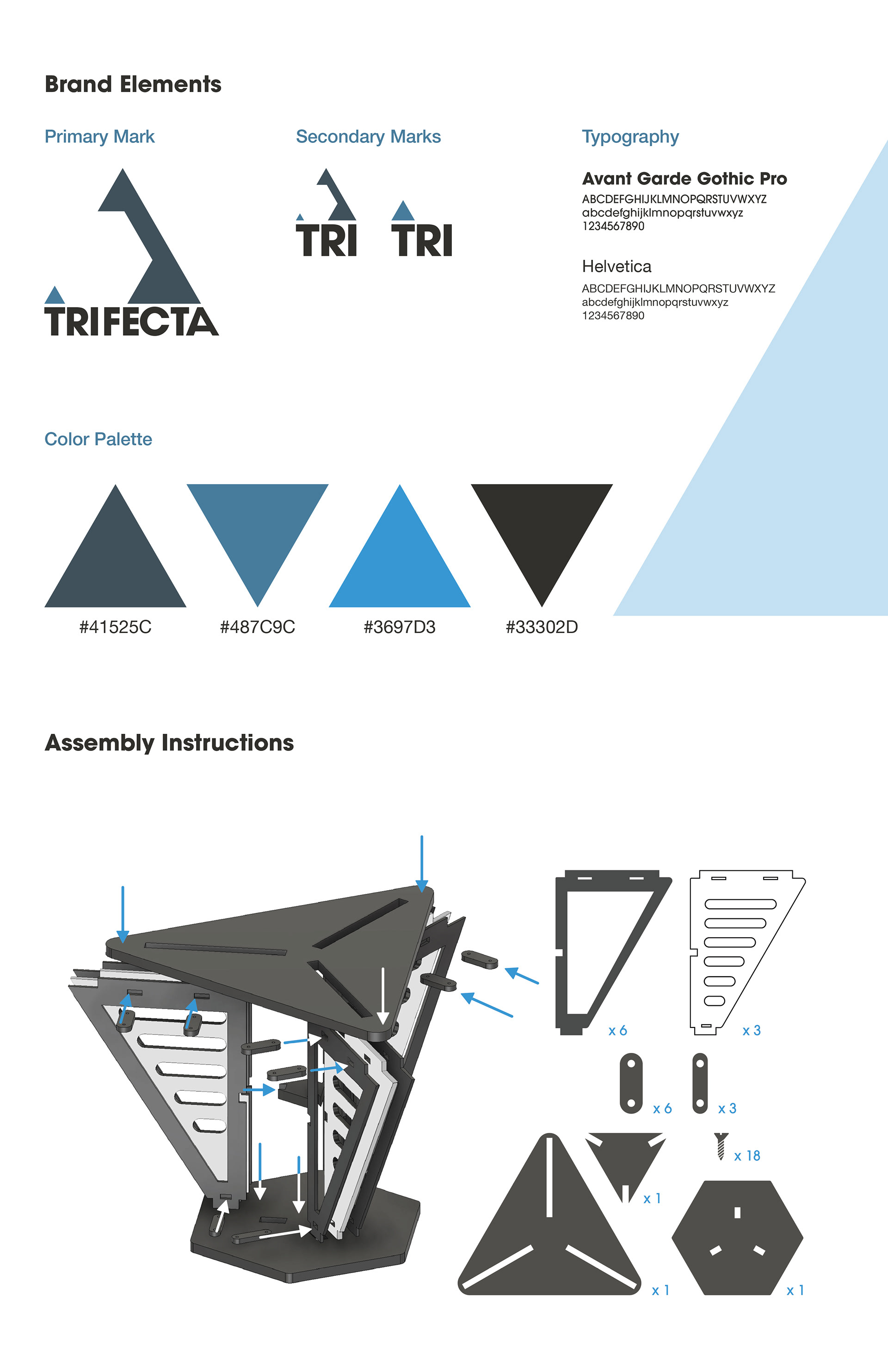
Reflection
I decided to take this section of the offered collaborative classes because it was completely out of my comfort zone. As a visual communication major, I haven't done much physical making since foundations. I cannot believe how much knowledge I gained about designing physical products and how to work confidently and safely in the woodshop in just one semester. I was definitely skeptical at first, but can genuinely say this has been such an enjoyable class and one that made me stretch beyond my major's specific skillset making me a much more well-rounded designer. I also got to work with two incredible peers of mine that I wouldn't have otherwise gotten an opportunity to work with which in itself was a huge benefit of the class. I am very proud of our final design and how much I learned throughout this semester and hope to keep expanding my physical-making skills.
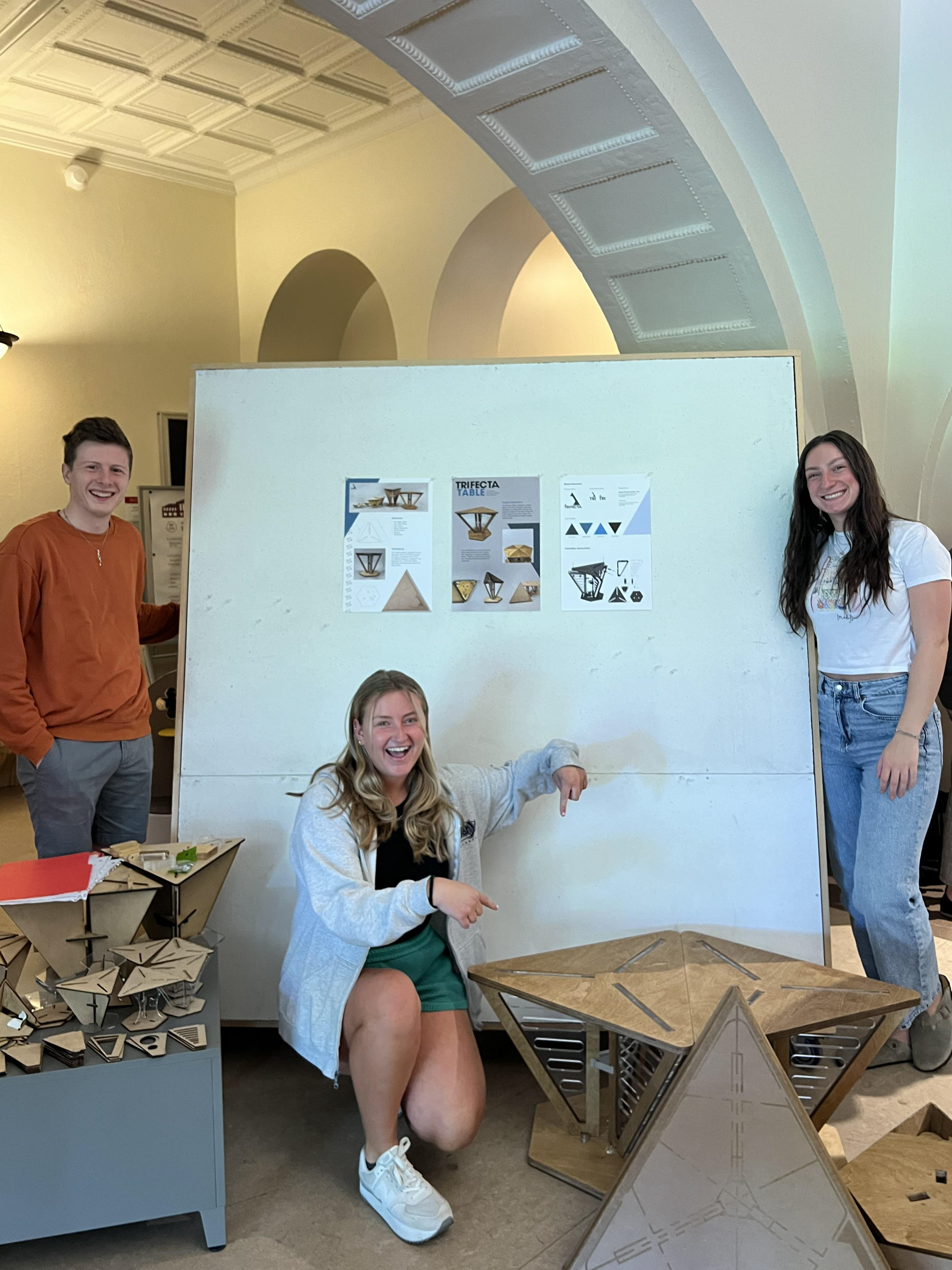